Applications of Powder Conveying Systems
Powder conveying systems are an essential component of many industrial processes, providing a cost-effective and efficient way to transport bulk materials. These systems are used in a variety of applications, from the food and pharmaceutical industries to the chemical and manufacturing sectors. In this article, we will explore the applications and benefits of powder conveying systems, and the impact they have on modern industrial operations.
Types of Powder Conveying Systems
Powder conveying systems come in a variety of types, each with its own unique set of advantages and applications. Pneumatic conveying systems, for example, use air pressure to transport powders through pipes or ducts. This is a popular option for industries that require a clean and hygienic method of powder transport, such as the food and pharmaceutical sectors. Another common type of powder conveying system is the screw conveyor, which uses rotating screws to move materials along a trough or tube. This system is well-suited to handling abrasive or fragile materials, making it a popular choice for the chemical and mining industries. Other types of powder conveying systems include belt conveyors, bucket elevators, and vibrating conveyors, each offering their own unique benefits and applications.
Powder conveying systems are used in a wide range of industrial applications, playing a crucial role in the efficient and reliable transport of bulk materials. In the food industry, for example, these systems are used to move ingredients and powders between processing stages, ensuring a smooth and continuous production process. In the pharmaceutical sector, powder conveying systems are used to handle delicate and often hazardous materials, providing a safe and hygienic method of transport. Powder conveying systems are also widely used in the chemical and manufacturing industries, where they play a key role in the movement of raw materials and finished products. With their ability to handle a wide range of materials, including powders, granules, and bulk solids, these systems are an essential component of modern industrial operations.
Comparison Table of Pneumatic Conveying Systems
Characteristic | Positive pressure dilute phase pneumatic conveying | Negative pressure dilute phase pneumatic conveying | Positive pressure dense phase pneumatic conveying | Nitrogen circulation pneumatic conveying |
Applicable scenarios | Distributed transportation from one location to several locations | Material collection should not produce dust, and materials should be taken from deep or low places. Concentrate feeding from multiple locations to one place | Large batch transportation, fragile granular material transportation Powder and granular material transportation | Potential explosive, radioactive,Oxidative materials |
Environmental isolation effect | Positive pressure system, isolating dust and rainwater | Negative pressure environment, no dust generated during material collection | Positive pressure system, with less material breakage and minimal wear and tear | Safe isolation to reduce the risk of dust explosion |
Operational stability | Stable and reliable flow pattern, velocity, and pressure | Dust is not easy to overflow | Suitable for fragile granular materials, simple separation and dust removal | Energy saving, nitrogen recycling and reuse |
energy consumption | general | low | low | energy conservation |
Material handling performance | general | Non dusty, suitable for materials with special requirements | Suitable for fragile materials with particle size less than 2mm | Suitable for hazardous materials |
Application scope of material conveying
industry | material |
---|---|
Petroleum and Chemical Industry | PP、PE、 Petroleum coke, potassium sulfate CaCO3、ABS、PVC、BaSO4、BPA、HDPE、CPE、EFP、EPC、EPVC、PVB、 |
PA6、PC、PET、PVA、 Melamine, potassium bromide, sodium bromide, ion exchange resin, thiamine, polyacrylamide, urea | |
Plastic pellets TPU、SAP、 Lithium cobalt oxide, polystyrene, dry rubber powder, compound fertilizer, adipic acid, diacetic acid tablets, monoamine phosphate, dicyandiamide | |
Polyformaldehyde, VD3 powder, etc | |
Building Materials | White carbon black, activated carbon, bleached soil, calcined kaolin, silicon carbide powder, talc powder, silica sand, zeolite, hydrated lime, rubber, quartz powder, carbon black |
Cement, wood powder, wood chips, hard asphalt, perlite powder, talc powder, sanding powder, phosphogypsum, dry mixed mortar, gypsum powder, dry sand, aluminate | |
Heavy calcium powder, graphite, zirconium aluminum beads, bauxite, white lime, white clay, sawdust, carbon, etc | |
Foodstuff | Wheat, soybeans, corn, fructose, apricot kernels (with shells), soybean meal, soybean skin, gluten powder, peanut red coat, milk powder, soybean flour, rice husk |
Starch, food grade xanthan gum, threonine, corn germ, flour, yeast powder, feed pellets, protein powder, bran, sesame, cassava starch | |
Rice, pectin, peas, dehydrated garlic flakes, distiller’s grains, rice bran, peanut cake, monosodium glutamate, cinnamon powder, coffee powder, maltodextrin, thirteen spice, etc | |
Metallurgical Minerals | Calcium carbide, silicon powder, bentonite, limestone powder, alumina, zinc roasted sand, iron concentrate powder, potassium feldspar powder, cordierite powder, stone powder, calcium oxide |
Titanium concentrate powder, bauxite powder, phosphate powder, etc | |
Non-ferrous Metal | Titanium dioxide, magnesium oxide, aluminum hydroxide, vanadium catalyst, titanium dioxide, aluminum oxide powder, potassium chloride, saltpeter, magnesium hydroxide, antimony oxide powder |
Copper concentrate powder, zirconium aluminum composite beads, aluminum fluoride, soda ash, etc | |
Medicine | Glucose, enzyme preparations, etc |
Chemical Fiber | Alkali fiber, etc |
Coal | Coal coke, lignite, coke powder, coal powder, etc |
Power | Fly ash, dust, cigarette ash, boiler slag, etc |
Steel | Metal ash, kiln ash, pyrite slag, vanadium catalyst, etc |
Environmental Energy | Calcium powder, carbide slag, desulfurization ash, etc |
LZL-200-GS Airflow Classifier
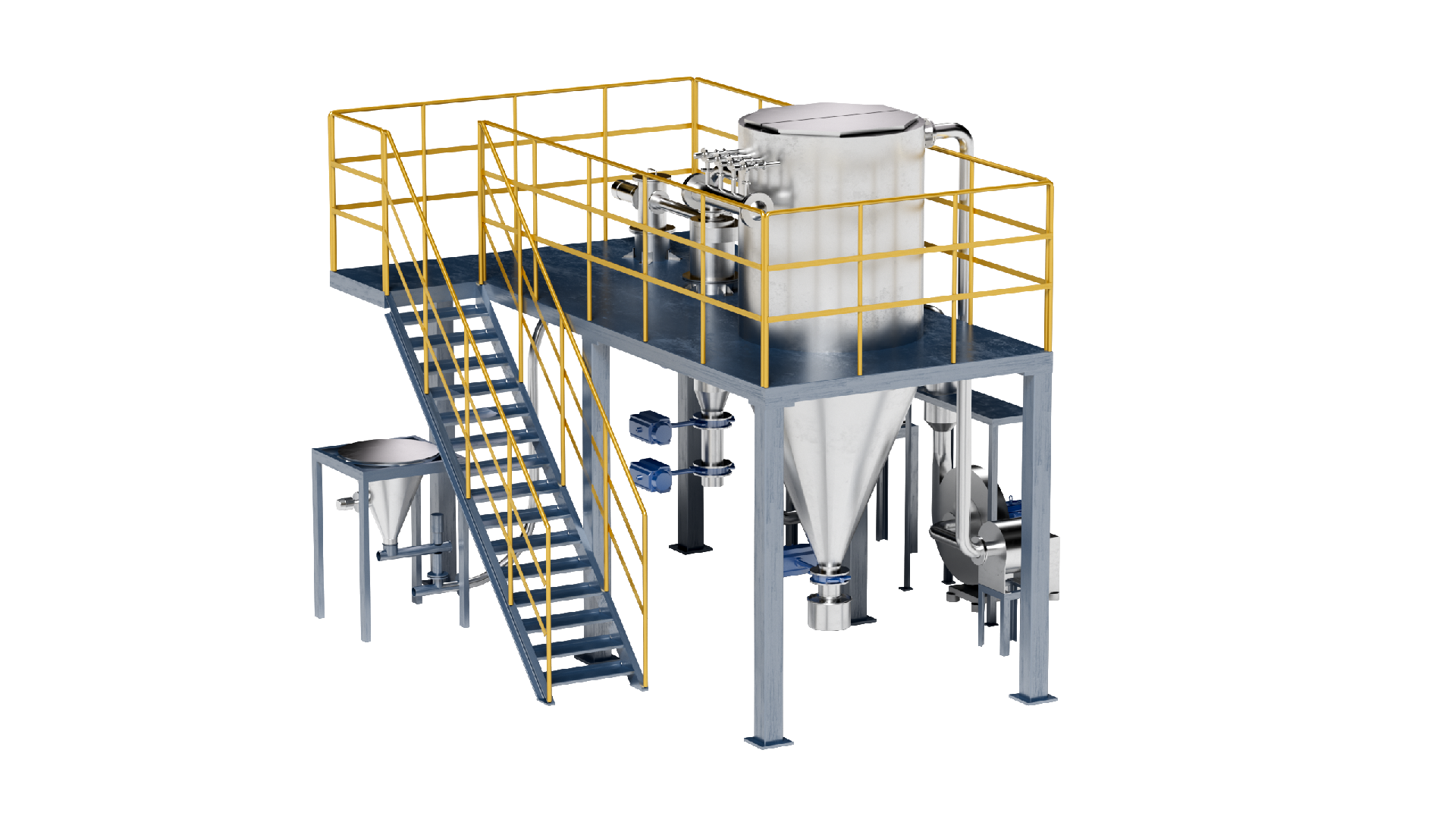
The LZL-200-GS air classifier shapes powders and removes ultra-fine powders. The equipment is fed from the pneumatic butterfly valve of the material in the raw material silo and sent to the main engine, and the material in the main engine is sprayed and depolymerized through the Laval nozzle, and the depolymerized material is graded by the grading wheel to the next grading wheel for compulsory classification, and the coarse powder is discharged through the double manual butterfly valve at the bottom of the breaking up host; The fine powder is collected by cyclone, and the solid-gas separation adopts a pulse dust collector.
I.Equipment advantages
raise the flow-type energy of the powder completely
Precise separation of the corresponding material sections
Suitable for all kinds of metal powders
Ultrafine powder separation can be realized
Open and closed grading can be realized
II.Device parameters
Capacity | 30~200kg |
Separation particle size | 3-100μm |
precision | ±1μm |
Gaseous medium | Nitrogen, helium |
Oxygen increase control | ≤60ppm |
Grading order | Up to 3 levels |
Air consumption | You can refer to the specific model data |
Packing specifications | Customizable |
Suitable for powder making furnaces | Gas atomization equipment, centrifugal atomization equipment |
LFAPL-150-EX-GS Flat 3D Milling Post-Processing Automation System
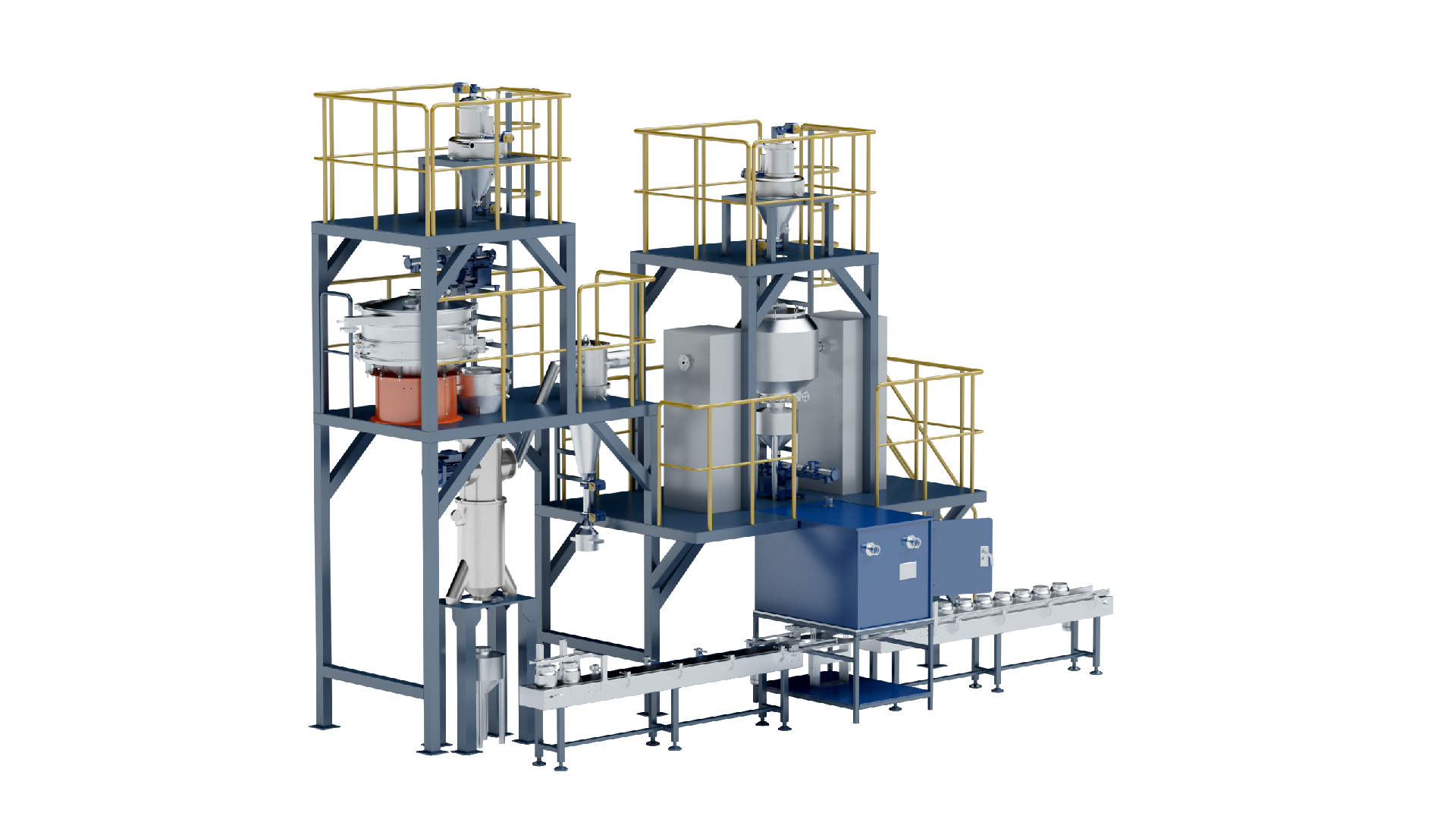
LFAPL-150-EX-GS is a professional equipment for 3D printing powder anaerobic automatic screening-grading-mixing and drying-oxygen-free packaging. The system includes vacuum feeding, ultrasonic screening, air classification, double cone drying and mixing, automatic packaging and other process equipment, and the whole production is carried out under oxygen-free closed conditions.
I.Equipment advantages
The fully enclosed and automated powder transfer process avoids the oxidation caused by the environment during the powder transfer process
High-precision powder screening and grading system
Mix large volumes of batches with heat drying
Fully automated, oxygen-free closed powder packaging process
High degree of automation, saving labor costs and reducing labor intensity
Small footprint and low energy consumption
Processes can be interchangeably connected in series
II.Device parameters
Capacity | 30~200kg |
Separation particle size | 3-100μm |
precision | ±1μm |
Gaseous medium | Nitrogen, helium |
Oxygen increase control | ≤60ppm |
Grading order | Up to 3 levels |
Air consumption | You can refer to the specific model data |
Packing specifications | Customizable |
Suitable for powder making furnaces | Gas atomization equipment, centrifugal atomization equipment |
LVAPL-200-EX-GS Vertical Powder Post-processing Automatic Production Line
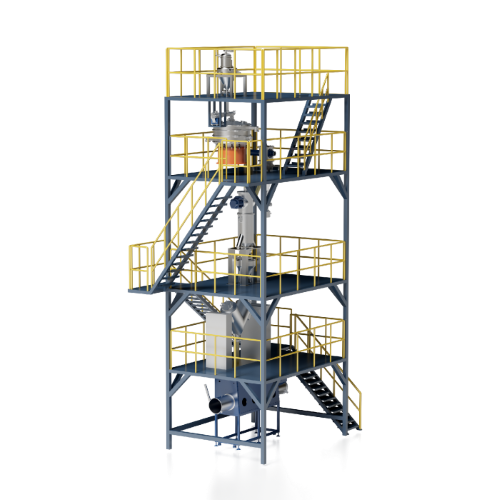
LVAPL-200-EX-GS vertical powder post-processing automatic production line adopts three-dimensional 3D powder post-processing automation system, which is a professional equipment for 3D printing powder anaerobic automatic screening-grading-mixing drying-oxygen-free packaging. The system includes process equipment such as vacuum feeding, ultrasonic screening, air classification, V-mixing, glove box packaging, etc., and the entire production is carried out under oxygen-free closed conditions.
I.Equipment advantages
The fully enclosed and automated powder transfer process avoids the oxidation caused by the environment during the powder transfer process
High-precision powder screening and grading system
Bulk batch mixing
Oxygen-free closed powder packaging process
High degree of automation, saving labor costs and reducing labor intensity
Small footprint and low energy consumption
Uniformity of powders
II.Device parameters
Capacity | 150~200kg |
Number of mesh screened | 100 mesh, 270 mesh |
voltage | 380V 50HZ |
power | 37kw |
Argon gas consumption | 20Nm³/h |
Compressed air consumption | 18Nm³/h |
Oxygen increase control | ≤120ppm |
Packing specifications | Customizable |
Suitable for powder making furnaces | Gas atomization equipment, centrifugal atomization equipment |
Installation height and footprint | 11m、5.4m |
LPPL-100-EX-GS Automatic Printing Powder Handling Line
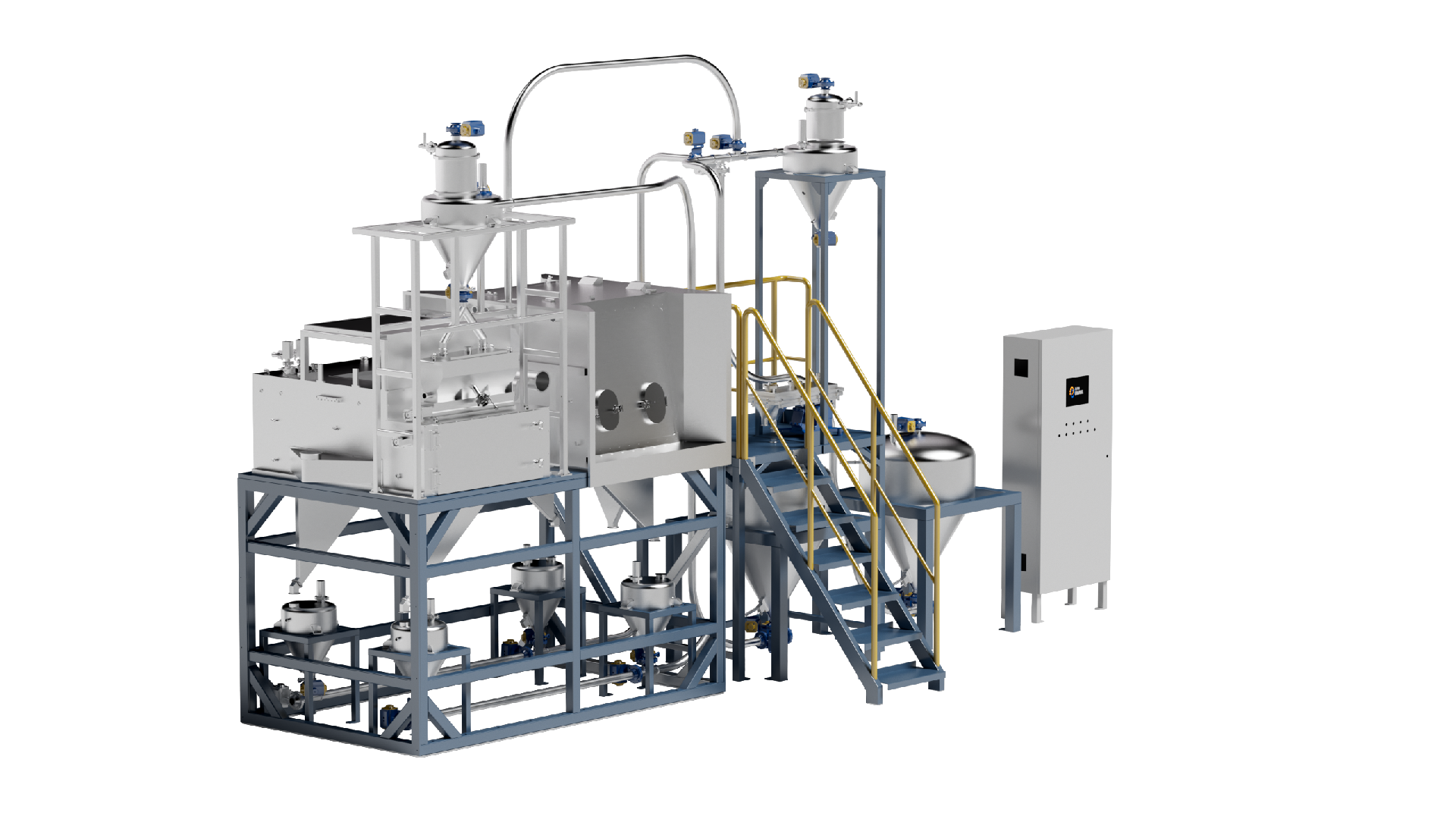
LPPL-100-EX-GS printing powder automatic processing line is a professional equipment for 3D printer powder automatic feeding – automatic recycling and sieving of old powder after printing, through the form of negative pressure pipeline transportation, the printed powder is sucked into the sieve station for impurity removal and then automatically backfilled to the printer buffer bin, the whole process is automatically operated and carried out under the protection of inert gas.
I.Equipment advantages
Accurate powder replenishment to the printer;
Avoid environment-induced oxidation during powder transfer;
Improved powder utilization;
High degree of automation, saving labor costs and reducing labor intensity.
II.Device parameters
Capacity | ≥150KG/H |
Number of mesh screened | 100-635 mesh; |
voltage | 380V 50HZ |
power | 10kw |
Argon gas consumption | 50Nm³/h |
Compressed air consumption | 18Nm³/h |
Oxygen increase control | <20ppm |
Vacuum Conveying Adapter (Vacuum Adapter)
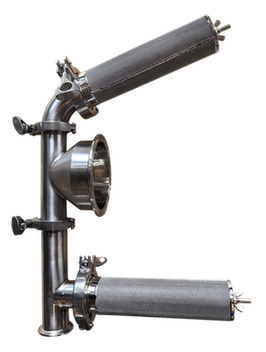
Vacuum conveying adapter is used with the feeding station and silo to dock negative pressure conveying and install adjustable air supply devices before and after installation to meet the adjustment requirements of negative pressure conveying on the amount of air supply.
Pneumatic Y-shaped three-way dispensing valve
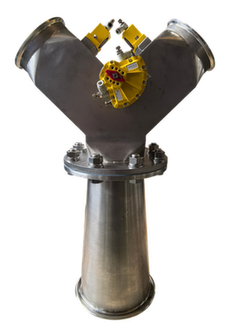
The pneumatic Y-shaped three-way distribution valve drives the valve core through the pneumatic actuator, and quickly switches the material flow direction in the Y-shaped valve body, so as to realize the diversion or merging control of one feed and two discharges. Its Y-shaped design effectively reduces material residues, especially suitable for the diversion of powders, granules and other materials.
Activated hopper
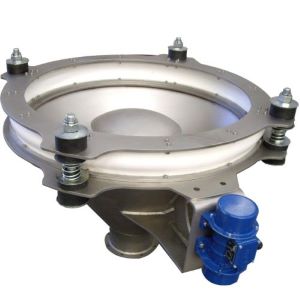
Activated hopper (also known as vibrating hopper) is a new type of feeding equipment, installed in the lower part of various silos, through vibration to activate the material, can effectively eliminate the arching, blockage and sticking of the material, to solve the problem of silo discharge.
I.Equipment advantages
1. Activate and loosen materials, smooth flow of materials, and no coal blockage;
2. Compact structure and low installation height, which can greatly save infrastructure investment;
3. All components are designed with long life, which is basically maintenance-free;
4. The feeding amount is adjustable online, which can be controlled remotely or locally.
5. Small power, large amplitude, simple structure, short maintenance cycle;
6. Neutralization and blanking, the belt does not deviate;
7. It has the function of uniform feeding and warehouse material cut-off, and there is no need to set up another gate;
8. Good sealing performance, even when the amount of coal is large, there will be no coal leakage;
9. The dynamic load of the equipment is small, the impact force is relatively small, and there are no special requirements for the foundation;
10. The equipment runs smoothly and reliably, with low noise and long life.
II.How it works
1. The principle of sub-resonance is adopted, and the excitation force is large. According to the theory of vibration and practical experience, the operating point of the activation feeder is in the sub-resonance range. In this way, it not only takes advantage of the characteristics of the equipment near the resonance point of large excitation force, but also avoids the resonance point, so that the equipment works without resonance, and greatly reduces the loss of the equipment.
2. The opening is a large square opening to avoid arching. According to the characteristics of coal, the phenomenon of material arching has a great relationship with the minimum size of the flow section of the silo, and has a small relationship with the flow section. The activation feeder adopts a large square opening, which maximizes the size of the two unilateral sides of the square while increasing the cutting area.
3. Special activation block design, large activation area. The activation feeder adopts a special activation block design, which organically combines and separates the blanking part and the activation part, so that the activation area of the upper part of the feeder is large, and the activation can reach 3~4 meters above the feeder inlet, so as to ensure that the coal is not blocked within the height range, and the blanking part is not subject to the pressure of the silo material, so as to ensure that the activated material falls freely and smoothly.
4. The matching of the material quantity and the activation amount is reasonable to avoid the more vibrating and more solid the material. The relationship between the amount of blanking and the amount of activation is designed reasonably to ensure that the amount of blanking is greater than the amount of activation, and there will be no accumulation of activated materials at the discharge port due to untimely blanking, resulting in agglomeration, thereby blocking the channel.
III.Application industry
It is widely used in new energy, chemical industry, building materials, ceramics, refractory materials, powder smelting, mining, metallurgy, thermal power, glass, cement, grain and other industries.
Airflow mixer
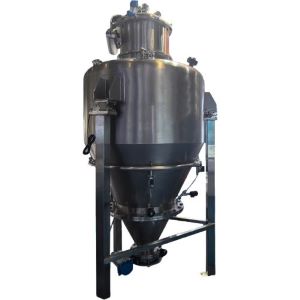
The compressed air is used to impact the material in a pulsed way to rise, diffuse and settle to achieve the purpose of full mixing and homogeneity in the shortest time.
The airflow mixer is mainly composed of compressed air source and air storage tank, suction (feeding) device, mixing silo and silo top dust collector, mixing and control device.
I.How it works:
The air tank for mixing control is filled with clean compressed air (in line with the operating pressure): the suction (feeding) device feeds the material into the mixing silo; PLC can be programmed to control the control valve/pneumatic control valve, and send compressed air (through the mixing head) into the mixing silo in the form of intermittent pulses, and the powder in the silo presents a spiral upward flow state under the action of pulsating airflow, and is thrown up and dislocated and falls; After several pulsed processes, the materials in the mixing silo are homogenized in a few minutes.
The compressed air enters the silo through the nozzle of the mixing head in a pulsed way, the compressed air spirals up, the material is impacted by the spiral rising compressed air, and the compressed air spirals up and expands together, and the material settles down after the compressed air expands to a certain extent, and a pulse mixing process is completed. After a pause for a few seconds after the end of one pulse, the mixing of the second pulse is started, and the pulsed compressed air drives the material to flip and roll (at the same time, there is diffusion mixing, convection mixing or mobile mixing, in which convection mixing or mobile mixing plays a major role) until the material is mixed evenly.
II.Peculiarity
Integrated negative pressure feeder for automatic feeding
Integrated weighing system to detect the incoming and outgoing status in real time
It adopts the form of spray plate, which is easy to install, and the air flow swirl rises, and the passage path is long
Set up a pressure detection unit to detect the mixing pressure in real time
There are no mechanical moving parts inside, and it is easy to achieve in-place cleaning
Set up a safety pressure relief device to ensure the safe operation of the equipment
III.Equipment advantages
Adapting to ultra-fine powder has a dispersion and depolymerization effect on pseudo-agglomeration
No mechanical parts, no risk of lubricating oil leakage, no friction, no heat
The homogenization speed is fast, and it only takes a few minutes to mix and homogenize a single batch
High degree of uniformity, multi-point sampling, accurate control
Large-capacity mixer, a single batch can mix 1-100m³ at one time
No dead ends, no residues, pulse cleaning is convenient, and there is no cross-contamination
Low energy consumption, low cost, unit energy consumption is only 30-50% of mechanical mixing
Micro-negative pressure operation, no dust pollution
IV.Application industry
Mainly used in chemical products, plastics, pharmaceuticals, battery materials, food, feed, cement, soil and stone, ceramic raw materials and other industries, with no leakage, no dead end, no pollution, sealed mixing, environmentally friendly characteristics, low maintenance cost, fast mixing speed, especially suitable for large quantities of materials rapid and uniform mixing operations.
Big bag unpacking machine
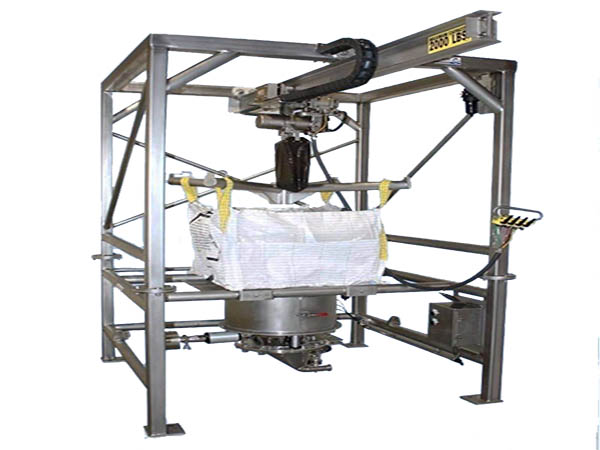
The ton bag unpacking machine is suitable for unpacking and unloading bagged powder and granular materials, and is widely used in food, medicine, new materials, battery materials, metal powder and other industries. The ton bag unpacking machine has the characteristics of reliable working performance and low power consumption, and it is especially suitable for toxic, flammable, strong corrosion, high dust and occasions that are not suitable for personnel to touch
I.How it works:
The unpacking machine itself is equipped with an electric hoist to hoist the material above the frame of the unpacking machine, and then slowly fall, the material bag is manually disassembled in the process of falling slowly by the blanking port or by the cross cutter (optional) to cut the bottom of the material bag, the material slides down by gravity, so that the powder and granular material in the ton bag falls into the storage hopper by gravity to complete the unloading work, and is designed with a slapping device. The device can effectively protect the production environment, reduce the work intensity of laborers, and also improve production efficiency, and solve the phenomenon that large bags are not easy to discharge due to moisture absorption caused by agglomeration and bridges in the opening of bags.
The discharge port of the unpacking machine can be combined with screw conveyor, belt conveyor, hoist and pneumatic conveying device. The dust-prone materials can be fully enclosed, and equipped with a special dust collector, and can also be connected with the on-site dust removal system.
II.Equipment advantages
The overall structure of the unpacking machine is compact, delicate and beautiful, easy to operate, and low power consumption.
The bottom beating device can better ensure the smooth discharge and prevent the material from being retained.
The ton bag unpacking machine is convenient and comfortable to operate, which effectively reduces the labor intensity of workers and improves work efficiency.
The dust control effect is good. The fully enclosed type can realize synchronous dust collection, and there is no dust leakage during the operation of the bag unpacker.
After unpacking, there is no residue of materials in the residual bag.
It can be equipped with a variety of follow-up conveying equipment (pneumatic conveying, spiral conveying, pipe chain conveying, belt conveying)
Screw metering big bag packing
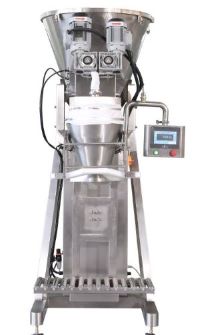
The screw filling machine is semi-automatic, suitable for quantitative filling of powder, small particles and other materials, easy to operate, small input cost, can be used for bagging, bottling and other packaging forms. Common products such as flour, protein powder, sugar, talcum powder, medicines, dyes, etc.
I.Equipment advantages
Servo motor and drive control screw, stable work, high precision
PLC control, touch screen interface, with hand wheel to adjust the height of the bin, easy to operate
All stainless steel construction, quick-release bin, screw and accessories, full weld mirror polish, easy to clean and maintain
The following configurations are available flexibly upon request
In-line heavy-duty filling to improve accuracy; dust removal device; anti-spillage valves; replacement of electrical accessories; Automatic feeding 316L corrosion-resistant material;
Screw feeder
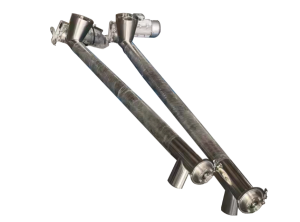
The screw feeder can convey powders and granules from one machine to another. It can be combined with the packaging machine to form a production line. It is mainly used for conveying powdered materials, such as milk powder, protein powder, rice flour, milk tea powder, solid beverages, coffee powder, sugar, glucose powder, food additives, feed, pharmaceutical raw materials, pesticides, dyes, flavors, spices, etc.
I.Structural features
The connection between the screw shaft and the hanging bearing, the head and tail shaft are embedded in the tongue type, and the installation and disassembly do not need to move axially, and the maintenance is convenient. The mandrel is long, the hanging is less, and the fault point is less.
The variable diameter structure is adopted to increase the volume of the hanging bearing to avoid contact between the lifting bearing and the material, and the life of the lifting bearing can reach more than two years.
Each transmission part adopts a floating connection mode, and the crane bearing is a universal joint structure, so that the spiral body, the crane bearing and the tail assembly form an integral rotary float body, which can be freely rotated and avoided with the conveying resistance within a certain range, without jamming or blocking.
The head and tail bearing seats are outside the shell, and all bearings adopt multi-layer sealing and matching sealing technology, so that the bearing has a long service life.
Compared with other conveying equipment, the screw feeder has the advantages of small cross-sectional size, good sealing performance, stable and reliable operation, multi-point loading and unloading in the middle, safe operation and easy maintenance.
II.How it works
The material weight signal from the metering screw is transmitted to the 3U403 (one machine with one DCS interface) or 3U600 (one machine with 16 channels) measurement and control system (both 3U403 and 3U600 have a microprocessor at the core). By continuously comparing the set value with the actual weight of the material conveyed by the screw, the speed of the steady flow spiral is constantly adjusted. As a result, the material flow is always stable at the set value.
Automatic feeding
All stainless steel construction, full welding and polishing
Quick-release barrel for easy maintenance and cleaning
Spiral reversal and bottom scrap outlet, easy to clean
The hopper can be vibrated or stirred
Square bin mixer
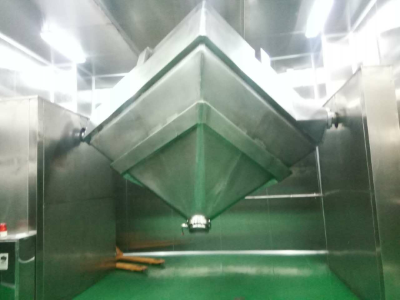
The machine is a new model that our company has successfully developed by looking at similar equipment at home and abroad, analyzing market needs, and combining its own advanced, mature and superior manufacturing conditions and technological means; Its structure is reasonable, the performance is stable, and the operation is convenient; The whole machine has no dead ends, no exposed screws, and a glossy and smooth appearance, which realizes the production safety of operation and the beauty of product appearance, and fully meets the GMP requirements of drug production.
I.Product principle
After the mixing hopper filled with materials is pushed into the rotary frame for positioning, the control system will send a signal for the hopper to be positioned in place, and then press the “confirm” button on the operation screen, and the clamping system will automatically lift the hopper into place and clamp it; After the hopper is clamped to the set position, the drive system mixes according to the set time, speed and other parameters; When the set mixing time is reached, the rotary frame automatically slows down and rotates slowly; When the slewing frame rotates parallel to the ground, it is immediately braked, and the mixing is completed; The clamping system then automatically lowers until the hopper is lowered to the ground; At the same time, the printer automatically prints the complete data of the batch of mixtures; That is, the mixing of a batch is completed.
II.Application field
It is mainly used for the mixing of solid particles and powders, granules and granules, powders and powders and other materials in the pharmaceutical industry, and is also suitable for the production process of powder materials in food, fine chemical and other industries. It has the advantages of good mixing effect and no cross-contamination and dust pollution.
Positive and negative pressure integrated conveying equipment
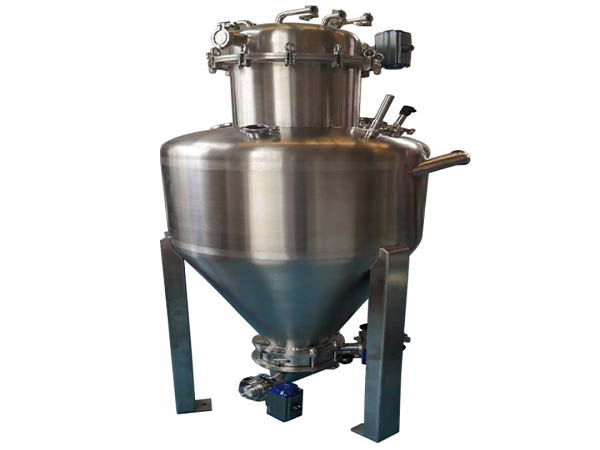
Positive and negative pressure dense phase conveying equipment is a new type of conveying equipment, which combines the functions of positive pressure and negative pressure conveying, and has the ability to extract materials that are not easy to send under negative pressure, and can be used as intermediate transfer and storage equipment to better optimize the production process.
I.Product principle
The positive and negative pressure hybrid conveyor integrates the function of negative pressure conveying and positive pressure conveying, the equipment is fed in the form of negative pressure, which can concentrate multi-point materials inside the equipment, and the output is in the form of positive pressure, which can send the materials to the required multiple target tanks or equipment
II.Equipment advantages
It combines the advantages of positive and negative pressure conveying to adapt to various working conditions;
The mechanism is simple, the failure rate is low, and WIP/CIP/SIP can be integrated;
The gas-material mixing ratio is high, the air consumption is low, and the diameter of the conveying pipeline is small
It is easy to automate, and it can realize the transfer of materials from multiple points to multiple points
The pipeline layout is convenient, there are no moving parts, and the operation is safer;
It is mostly used for the technical transformation of the production line and the installation of equipment with limited space
Positive and negative pressure integrated conveying equipment
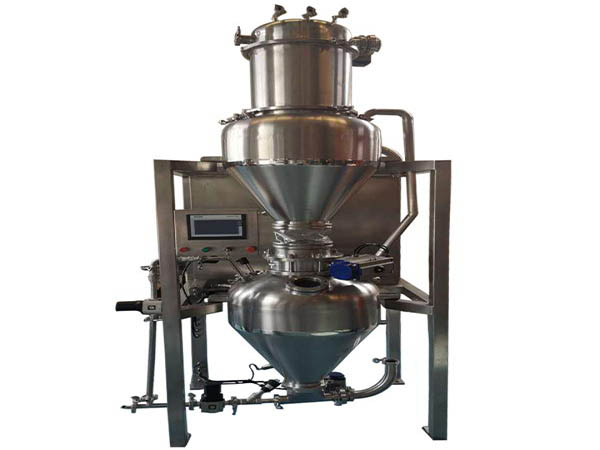
Positive and negative pressure dense phase conveying equipment is a new type of conveying equipment, which combines the functions of positive pressure and negative pressure conveying, and has the ability to extract materials that are not easy to send under negative pressure, and can be used as intermediate transfer and storage equipment to better optimize the production process.
I.Product principle
Due to the pressure action, the material enters the conveying pipeline from the sending tank, and the compressed air forms a pulse air flow (air knife) through the opening and closing of a certain frequency of the solenoid valve, and the material is cut into a material plug with the help of the air flow (air knife) pressure is greater than the pressure of the sending tank, and the material is pushed forward by relying on the static pressure before and after the material bolt is propulsed, and after the material and gas separation are implemented by the separation device, the material falls into the silo, and the gas is discharged into the atmosphere to achieve transportation
II.Equipment advantages
Long conveying distance, large conveying pressure and large production capacity;
The feeding device mechanism is simple and the failure rate is low;
The gas-material mixing ratio is high, the air consumption is low, and the diameter of the conveying pipeline is small
It is easy to automate, and can realize continuous or intermittent conveying, and can realize the transfer of materials from one point to multiple points
It can realize the conveying of materials from one point to multiple points, and the three-way valve can be quickly switched.
Twin spiral belt mixer
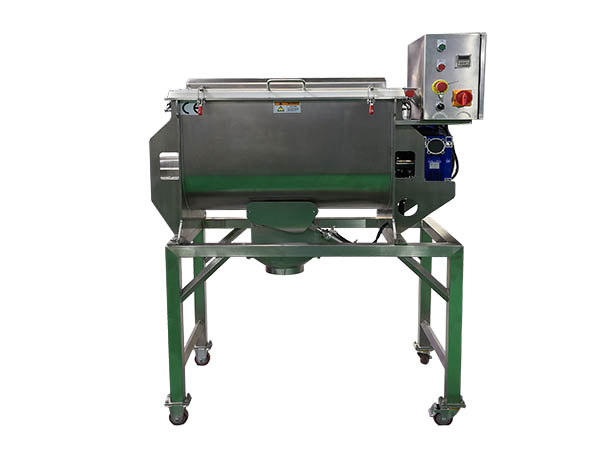
Double screw belt mixer is suitable for food, chemical, agricultural, pharmaceutical and other industries; It is suitable for mixing a variety of different materials such as powder, small particles, etc. When mixing, the inner spiral belt turns the material outward, and the outer spiral belt pushes the material inward, which can achieve a good mixing effect in a short time. It has the characteristics of good mixing and homogenization ability, high production efficiency, and extremely low failure rate.
I.Equipment advantages
1.It has a wide range of applications, and can be mixed with solid (powder and powder), solid and liquid (powder and liquid), and liquid and liquid.
2.High mixing uniformity: It can make the materials with a ratio of 1:10,000 times evenly mixed, especially for the mixing of materials with large specific gravity characteristics.
3.Fast mixing speed and high efficiency. 6-10 times more efficient than other mixers
4.Discharging is fast and convenient, usually 2~5 minutes to finish a batch of materials
5.The mixing process is mild, and the original state of the material is basically not destroyed
6.There is no pollution to the material, the mixing mechanism of the equipment is integral, safe and reliable, all edges and corners of the weld transition smoothly, easy to clean; The lubrication part is outside the barrel, and there is no dripping oil and abrasive debris penetrating into the material, which can be sealed to isolate the dust in the air from entering the material.
7.Low energy consumption and large loading factor.
8.The requirements for the plant are low, the equipment is horizontal, and various forms of driving devices and discharging positions can be arbitrarily selected, which is not restricted by the height of the plant and the floor space.
9.The equipment runs smoothly and reliably, with few wearing parts, long service life, convenient maintenance and simple operation.
II.Scope of application
It is used in the mixing of pesticides, veterinary drugs, food, chemicals, biology, aquaculture, ceramics, refractories, plastics, compound fertilizers and other solid-solid (i.e., powder and powder) solid-slurry (i.e., powder and glue slurry), and is also especially suitable for the mixing of viscous materials
Dust-free feeding station for small bags
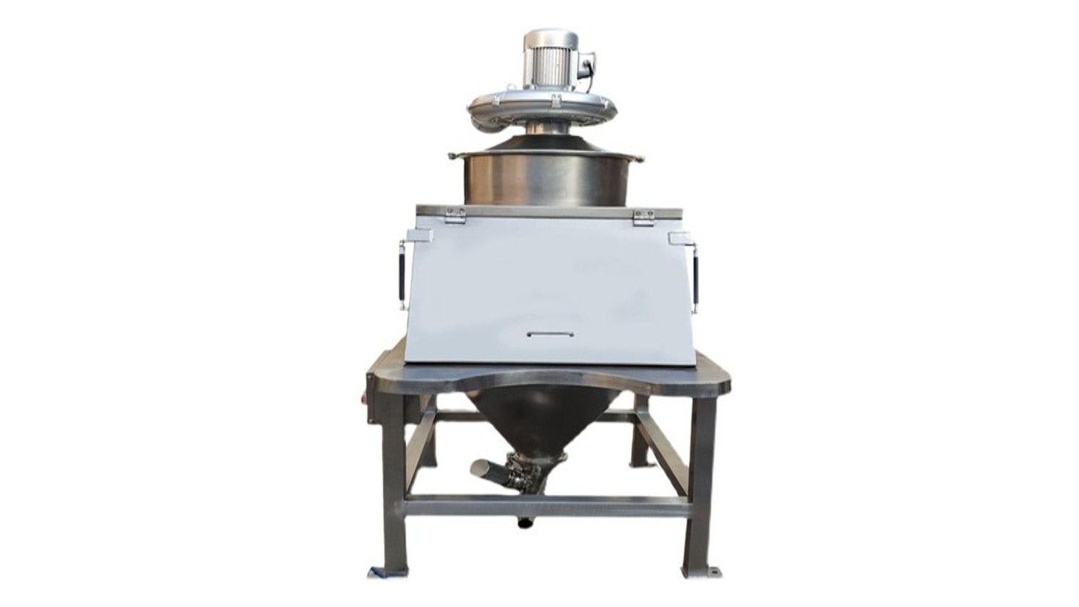
The small bag dust-free feeding station is a equipment used for feeding bagged or barreled powder and granular materials within 50KG. According to the process requirements, it can be used with vibrating hopper or stirring hopper for unloading, which is used for unloading small bags of powdery materials that are not easy to flow.
I.How it works
The operator places the bag on the stand and pushes it into the grid. Then, the operator cuts a vertical opening in the bag, and dumps the shake bag to empty it, and the material falls into the hopper by power, and can be connected with the conveying unit equipment through the conveying pipe at the bottom, and the material is output to the specified position. The built-in induced air dust collector collects dust from the dust produced during the bag emptying process. The filter is cleaned by a reverse compressed air jet, and the cleaned dust falls back into the hopper for continuous feeding.
The small bag feeding station, also known as the dust-free feeding station, is a kind of equipment used for unloading small bag powdery materials, which has the function of reducing the discharge dust, and the equipped vibrating screen has the function of filtering foreign matter.
II.Advantages of the design of the pouch dust-free feeding station
1.The calculated air volume and filtration area adaptation ratio make the air speed of the feeding port optimal, which not only captures the overflowing dust but also reasonably reduces the dust adhesion concentration of the filter cartridge;
2.Ergonomic design, the height of the feeding port is about 0.75 meters, which is more convenient and easy to feed;
3.Gas spring auxiliary opening and closing of the warehouse door is more labor-saving;
4.The filter bracket can prevent sundries such as bags or scissors from being mistakenly put into the silo;
5.Three-tube independent pulse backflush design to ensure the backflush effect and filter life;
6.It can increase the sound and light alarm function of the bottom material level, and automatically remind the workers to feed when there is no material;
7.According to the actual use of the project, non-standard design dimensions and installation methods;
8.Wide range of application, to meet the feeding of all solid materials.
III.Features
Simple structure, easy to operate, easy to maintain and operate;
Realize fully enclosed bag opening and pipeline transportation;
No dead angle design, easy to clean;
Automatic dust collection system to avoid dust flying and improve the working environment;
The same specification of bag opening station can be applied to different processing capacity requirements;
Suitable for all industries involving powders, such as food, chemical industry, battery, etc.
Powder vacuum feeder
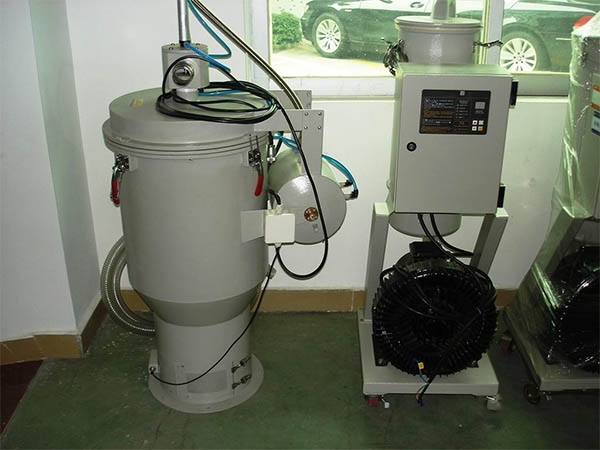
The powder vacuum feeder uses a single air as the power source, which is an intrinsically safe explosion-proof equipment, a dust-free closed pipeline conveying equipment that transports particles and powdery materials with the help of vacuum suction, which can eliminate dust environmental pollution, improve the working environment, and reduce the pollution of materials by the environment and personnel, and improve cleanliness.
I.How it works
Using the vacuum conveying principle, various powders and granules can be conveyed from the storage container to the hopper of any plastic machine. It can be used in conjunction with profile units, compounding systems, and chemical processing equipment. It is equipped with a pneumatic fan valve and a discharge auxiliary air valve, which can make the discharge more smooth; As well as the back-flushing sealing valve and high-pressure back-blowing device, so that the back-blowing effect is better; 6 sets of filter elements and special filter element lamination are used to make the filtration area larger and the filtration effect better; Convenient quick-release design, easy to clean and repair. It completely replaces manual feeding, realizes fully enclosed automation in the production process, and is safe, reliable, green and environmentally friendly.
II.Peculiarity
1. Adopt microchip control technology, which has the characteristics of accurate control, easy operation, and multiple alarm prompts;
2. Imported dust interception filter device is adopted, which has the characteristics of high strength, good dust interception effect, green environmental protection, etc.;
3. Equipped with pulse compressed air backflush cleaning device, the cleaning effect is better;
4. The suction port is automatically closed at the suction port when the blowback is blown, and there is no dust and no pollution;
5. The vibrating discharge system can effectively prevent bridging, and the discharge is more uniform and stable;
6. It can be equipped with 1-7 vacuum hoppers, which is suitable for a pair of multiple raw materials to be transported to the extruder or storage tank/replenishment bin over a long distance;
7. It has the characteristics of easy cleaning, easy disassembly, easy maintenance, no noise, etc.;
8. Realize automated, unmanned and green production, and effectively reduce labor costs.
Vacuum feeder
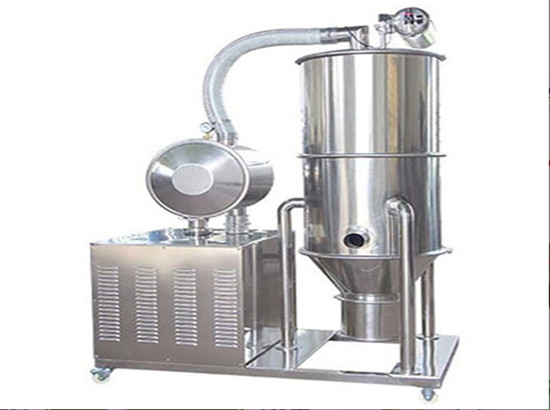
Vacuum feeder is a kind of dust-free closed pipeline conveying equipment that uses vacuum suction to transport particles and powdery materials, and uses the air pressure difference between vacuum and environmental space to form gas flow in the pipeline and drive the movement of powdery materials, so as to complete the transportation of powder. The foreign vacuum technology introduced by China has been continuously improved and improved, and is now widely used in chemical, pharmaceutical, food, metallurgy, building materials, agricultural and sideline industries and other light and heavy industries.
I.How it works
A vacuum generator or vacuum pump is used to generate a vacuum, and the negative pressure generated by the vacuum sucks the material from the inlet. The air is then separated from the material in the filter bin of the separator vessel. The material falls automatically due to gravity and is collected in the silo. Our cyclones prevent fine powders from entering the filter to improve the efficiency of the filter. When the silo is full of material, the vacuum pump automatically shuts down, and the pressure in the conveying equipment reaches equilibrium. The discharge valve is opened, and the material flows out through the discharge port and falls directly into the storage container. When discharging, the filter element is automatically cleaned by a back-blowing air bag. If the material is more viscous, we can install a special vibrator to assist in discharging. At the end of the blanking, the discharge compartment is automatically closed, and the whole conveying process is started again.
II.Equipment features:
1. Smooth modular design: The modular design not only makes the installation and maintenance simpler, but also more convenient to disassemble and wash, and eliminates the existence of dead ends. When cleaning, the design of the clamps between the various modules of the equipment allows the conveyor to be easily removed and installed. The equipment does not have gaps and dead corners that are easy to accumulate materials.
2. Fluidization device: The fluidizer is to produce a layer of air mold between the material and the inner wall of the conveyor silo, through which the air film can effectively help the flow of materials with poor fluidity, which not only prevents the material from bridging, but also improves the unloading efficiency. The fluidizer material is sintered polyethylene, which meets the requirements of FAD.
3. Back-blowing system: built-in one-to-one back-blowing airbag, pulsed gas back-blowing, each cycle can efficiently clean the filter, making the equipment performance more stable.
4. Filtration system: Japan Toray polyester coated filter element anti-static filter element, filtration accuracy up to 0.3 μm, maximum working temperature 130°C. Imported from Japan, it can be cleaned with alcohol, water, and compressed air, and can be used repeatedly for a long time.
5. Intelligent control system
III.How it worksScope of application
1. Food industry additives, candy, cocoa pills, cocoa powder, crystals, etc.
2. Industrial raw materials, waste materials and other materials, agricultural bulk materials.
3. Powdered materials, granular materials, mixed materials, tablets, capsules, etc. in the pharmaceutical industry